Instrumentation engineering is a specialized branch of engineering focused on the design, configuration and management of instruments and control systems. These systems are vital for monitoring and regulating industrial processes, ensuring accuracy, safety and efficiency in various applications, from manufacturing to energy production facilities.
In this section, we explore the principles and practices of instrumentation engineering, offering in-depth knowledge on sensors, transducers, control systems and data acquisitions. Whether you are new to the field or looking to advance your understanding, this resource is crafted to equip you with the essential tools and insights needed to excel in instrumentation engineering.
'Ctrl F' to find specific words on the website to hopefully streamline your learning and keep things quick and simple.
Why Instrumentation?
Electrical instrumentation refers to the tools and devices used to measure, monitor, and control electrical parameters such as voltage, current, resistance, power, temperature, and pressure in various engineering processes. It plays a crucial role in ensuring that electrical systems and machinery operate efficiently, safely, and within their designed specifications.
Key Functions of Electrical Instrumentation:
-
Measurement: Instrumentation allows engineers and technicians to measure key variables in a system. This can include monitoring voltage, current, temperature, and flow rates in complex processes.
-
Control: In many systems, electrical instrumentation helps regulate processes by controlling parameters automatically (e.g., adjusting power based on temperature readings).
-
Safety: Instruments are essential for ensuring that systems don't exceed safe limits, preventing malfunctions, overheating, or catastrophic failures.
-
Data Collection and Analysis: Electrical instruments collect data that can be used to analyze performance, troubleshoot issues, or optimize systems for energy efficiency.
-
Automation: In industrial settings, electrical instrumentation is key to automating processes, reducing human error, and enhancing productivity.
Why It's Used in the Engineering Industry:
-
Precision and Accuracy: Electrical instrumentation allows for highly accurate measurements, essential in fields like manufacturing, energy, and robotics, where small deviations can lead to failures or inefficiencies.
-
Efficiency: By continuously monitoring and adjusting system parameters, instruments help optimize performance, saving time, energy, and resources.
-
Process Control: Industries like oil and gas, pharmaceuticals, and power generation rely on precise control of electrical systems to ensure their processes run smoothly.
-
Predictive Maintenance: By monitoring the condition of equipment, instrumentation can predict when maintenance is needed, reducing downtime and avoiding costly repairs.
-
Safety Compliance: Many industrial systems must meet strict safety regulations. Electrical instrumentation helps ensure that systems are within legal and safe operating limits.
Overall, electrical instrumentation is fundamental to modern engineering, providing the means to maintain and control complex systems effectively.
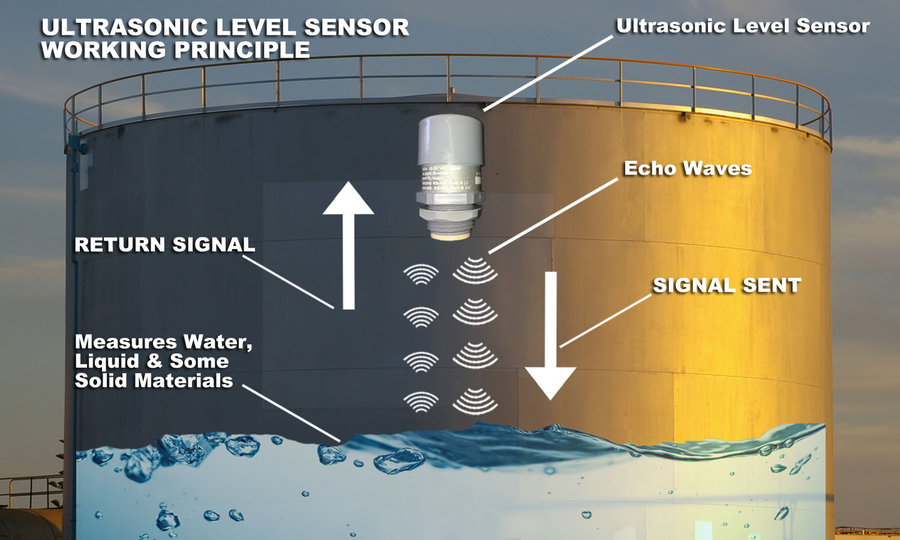
Measurement Principles
Measurement principles refer to the fundamental techniques used to quantify physical variables such as temperature, pressure, flow, and level. These principles provide the foundation for choosing appropriate instruments and methods for accurate data collection in various applications.
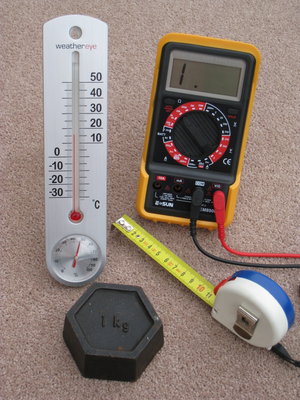
Electrical Meters
Electrical meters, such as voltmeters, ammeters, and multimeters, are devices used to measure electrical parameters like voltage, current, and resistance. They are essential for diagnosing and maintaining electrical systems by providing precise readings for troubleshooting and system optimization.
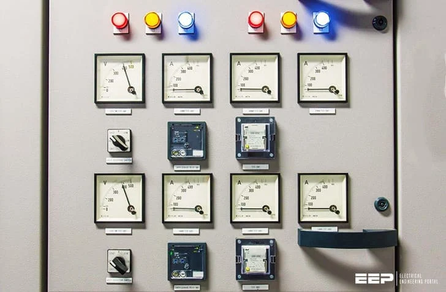
Signal Conditioning
Signal conditioning involves modifying or converting sensor signals into a format that can be interpreted by other systems. This includes amplification, filtering, or isolation to ensure accurate data transmission and processing, especially in systems prone to noise or signal degradation.
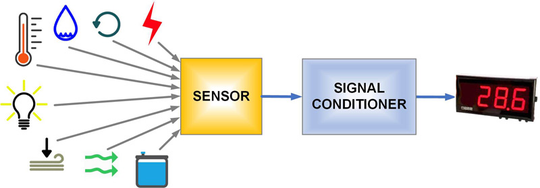
Transducers and Sensors
Transducers and sensors are devices that convert physical quantities (like pressure, temperature, or force) into measurable electrical signals. Sensors detect changes in their environment, while transducers convert these changes into signals for monitoring, control, or data analysis.
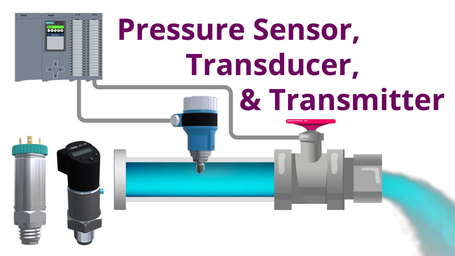
Data Acquisition Systems
Data Acquisition Systems collect, digitize, and analyze data from sensors and instruments. DAQs are used in various applications, from industrial automation to research, providing real-time data monitoring, analysis, and storage.
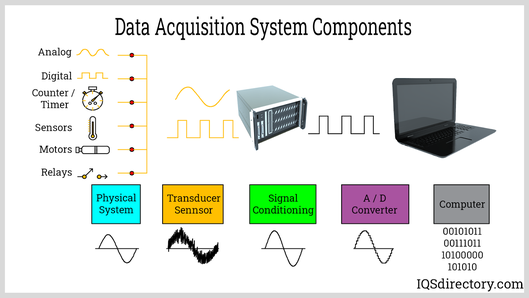
Calibration and Standards
Calibration ensures that instruments provide accurate readings by comparing them against known standards. Regular calibration against recognized standards ensures measurement consistency, accuracy, and compliance with industry regulations.
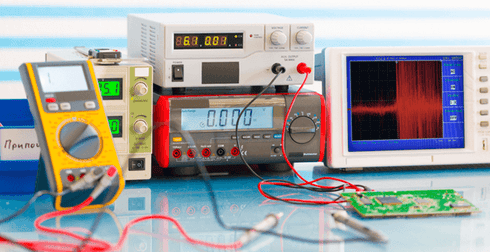
Control systems
Control systems automate processes by using feedback from sensors to regulate variables like temperature, pressure, or flow. They can be open-loop (manual) or closed-loop (automatic) systems, playing a critical role in maintaining stability and efficiency in industrial and manufacturing environments.
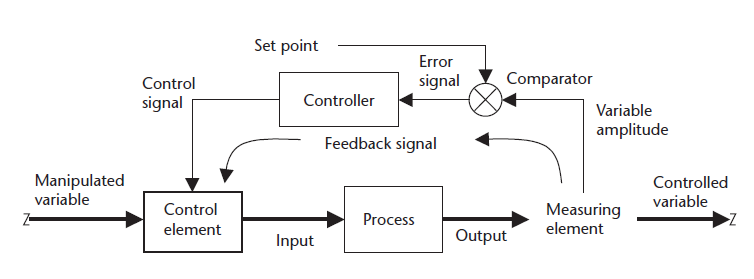
Analog and Digital Instruments
Analog instruments display measurements in a continuous format, like a needle on a dial, while digital instruments provide discrete numeric readouts. Both types serve different applications, with digital instruments offering more precision and integration into modern automated systems.
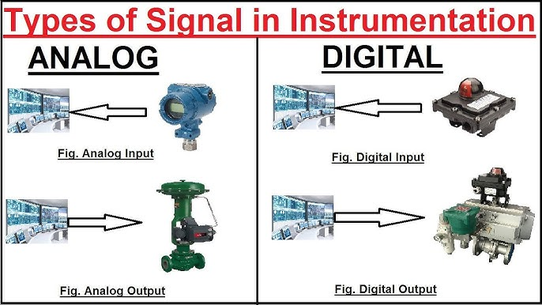
Signal Processing
Signal processing involves the analysis, interpretation, and manipulation of signals received from sensors and transducers. It improves data quality, removes noise, and extracts useful information, ensuring accurate and reliable measurement results.
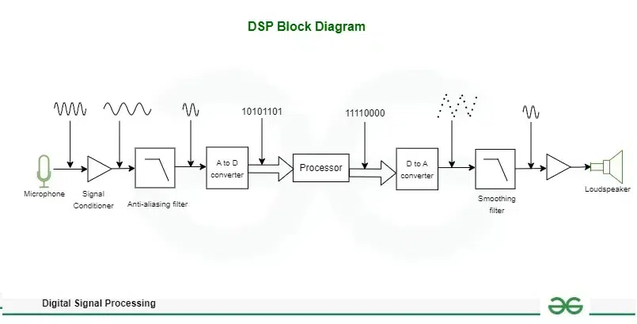
Process Instrumentation
Process instrumentation includes the devices and systems used to monitor and control industrial processes. Instruments such as flow meters, pressure gauges, and level sensors ensure processes run smoothly, safely, and efficiently by providing real-time data and control capabilities.
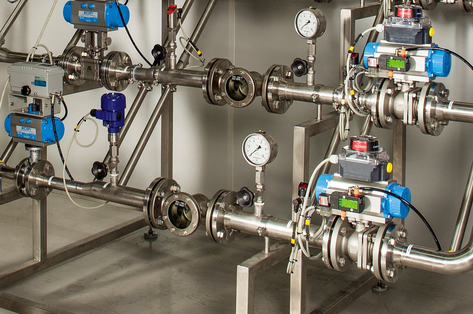
Instrumentation communication protocols
Instrumentation communication protocols, such as Modbus, HART, and Profibus, standardize data transmission between devices and systems. They ensure that sensors, controllers, and actuators communicate effectively in industrial automation systems.
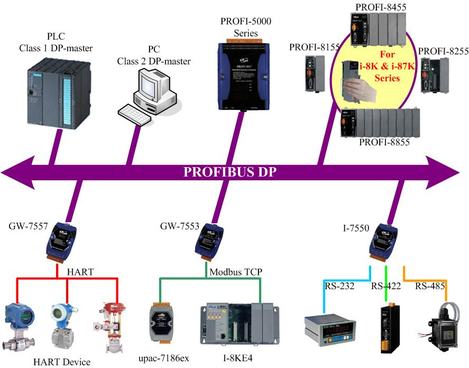
Safety in instrumentation
Safety in instrumentation involves ensuring that measurement and control devices operate reliably without causing harm to people or equipment. This includes using intrinsically safe designs, regular maintenance, and adherence to safety standards to prevent accidents, particularly in hazardous environments.
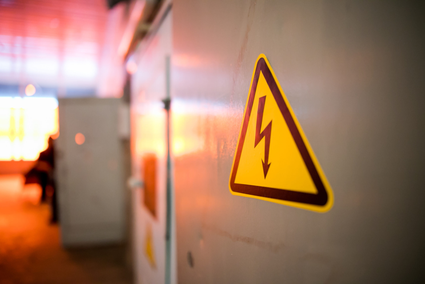
Safety Protocols and Regulations
Involves safe monitoring and control of processes using precise equipment, ensuring compliance with regulations for hazardous environments like ATEX and DSEAR.
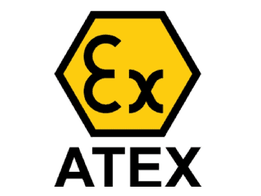