Instrumentation Communication Protocols: MODBUS, HART, PROFIBUS, and PROFINET
In industrial automation and process control, communication between field devices (sensors, actuators) and control systems (like PLCs or Distributed Control Systems (DCS)) is crucial for monitoring and controlling processes. Several standardized protocols exist to facilitate this communication, with the most commonly used being MODBUS, HART, PROFIBUS, and PROFINET. Each protocol offers distinct capabilities, depending on the application's requirements for speed, data handling, and real-time control.
Helpful Link(s):
https://youtu.be/YxF9QgRAx8A?si=xme5QClS4Z3R0wn8
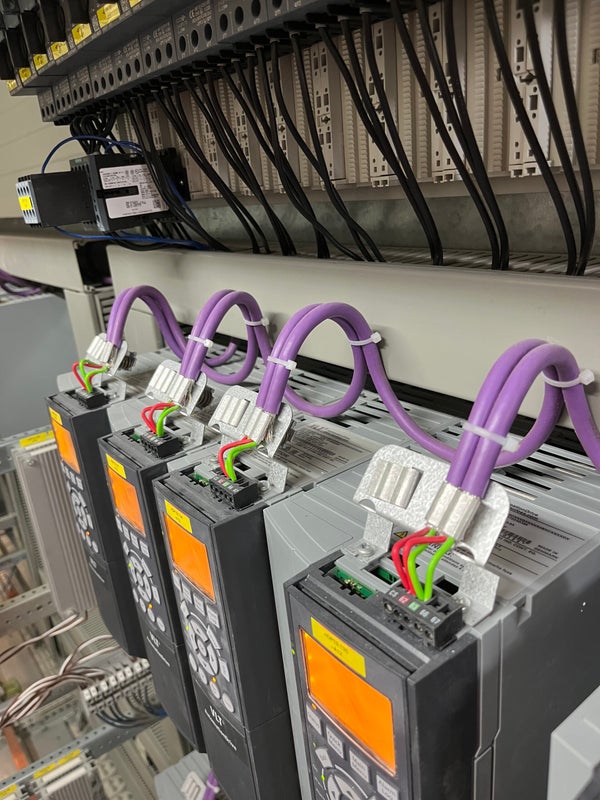
1. MODBUS Protocol
Overview: MODBUS is a master/slave or client/server communication protocol that was developed in 1979 by Modicon (now Schneider Electric). It was designed to communicate between industrial devices such as PLCs, sensors, actuators, and HMIs (Human-Machine Interfaces). It remains one of the most widely adopted communication protocols in industrial automation.
Types of MODBUS:
-
MODBUS RTU (Remote Terminal Unit): A serial communication protocol that uses binary encoding for data transmission over RS-232 or RS-485.
-
MODBUS TCP/IP: Used for communication over Ethernet networks, allowing MODBUS to be integrated into modern network infrastructures.
How MODBUS Works:
-
Master/Slave Model: The master device (usually a PLC or DCS) sends a request to a specific slave device, and the slave replies with the requested data.
-
Registers and Coils: Data is transmitted in units called registers (holding data such as temperature readings) and coils (digital inputs/outputs like control signals).
Integration with PLCs: MODBUS is commonly used in PLC systems where a PLC acts as the master device, collecting data from various sensors and sending control signals to field devices like motors or valves. Many modern PLCs come with built-in MODBUS support or allow for MODBUS integration via additional communication modules.
Applications:
-
Factory Automation: MODBUS RTU is widely used for connecting PLCs with field devices like motor controllers and temperature sensors.
-
Process Control: MODBUS TCP/IP is ideal for modern process control systems where data needs to be transmitted over long distances through Ethernet networks.
Advantages:
-
Simplicity: Easy to implement and widely supported.
-
Low-Cost: It is an open protocol, making it cost-effective.
-
Compatibility: Many PLCs and field devices support MODBUS, making it easy to integrate.
2. HART Protocol (Highway Addressable Remote Transducer)
Overview: The HART Protocol is a hybrid protocol that allows for both analog (4-20 mA) and digital communication over the same wiring. Developed in the late 1980s, HART is widely used in process industries for calibrating, configuring, and diagnosing field devices.
How HART Works: HART uses the 4-20 mA analog signal to transmit the primary process variable (like pressure, temperature, or flow) while simultaneously superimposing a digital signal that carries additional information (e.g., diagnostics, device health). This allows operators to communicate with smart instruments without disrupting the analog signal used for control.
Integration with PLCs: In a typical setup, a PLC collects the analog signal (4-20 mA) from HART-enabled devices, while the digital signal can be used for diagnostics or configuration. This provides flexibility to monitor the health of smart devices or adjust settings remotely without affecting the process control system.
Applications:
-
Process Control: HART is often used in chemical plants, refineries, and oil & gas operations to communicate with smart instruments that provide real-time data for monitoring and troubleshooting.
-
Device Calibration: A HART handheld communicator can be used to calibrate field devices without disrupting the analog control signals.
Advantages:
-
Dual Functionality: Simultaneous analog and digital communication.
-
Easy to Integrate: Can work over existing 4-20 mA wiring, making it simple to retrofit legacy systems.
-
Diagnostics: Provides advanced diagnostics for predictive maintenance and troubleshooting.
3. PROFIBUS (Process Field Bus)
Overview: PROFIBUS is a fieldbus protocol developed in the 1980s by Siemens and is widely used in factory and process automation. It offers robust and high-speed communication between field devices and control systems, with PROFIBUS DP and PROFIBUS PA being the two most common variations.
Types of PROFIBUS:
-
PROFIBUS DP (Decentralized Periphery): Used primarily in factory automation for high-speed communication between PLCs and field devices (sensors, drives, etc.).
-
PROFIBUS PA (Process Automation): Used in process industries where communication is needed in hazardous environments. It operates at lower speeds but is designed for intrinsic safety in explosive environments.
How PROFIBUS Works: PROFIBUS uses a bus topology, meaning all devices are connected in parallel on a single cable. The protocol supports deterministic real-time communication, which ensures data is transmitted within predefined time limits—critical for process control applications.
Integration with PLCs: PLCs frequently act as master devices in PROFIBUS DP systems, controlling sensors, actuators, and HMIs. The deterministic nature of PROFIBUS ensures precise, real-time control, which is crucial in applications like assembly lines and high-speed manufacturing.
Applications:
-
Factory Automation: PROFIBUS DP is ideal for connecting a large number of devices (e.g., sensors, HMIs, motors) in an industrial environment where high-speed and reliable communication is required.
-
Process Automation: PROFIBUS PA is commonly used in the oil & gas and chemical industries, where intrinsically safe communication is essential in explosive environments.
Advantages:
-
High-Speed Data Transfer: Supports data rates up to 12 Mbps, ideal for real-time control.
-
Robust and Reliable: Designed for industrial environments, making it resistant to interference.
-
Scalability: Can support large networks with many field devices.
4. PROFINET (Process Field Network)
Overview: PROFINET is a modern, Ethernet-based industrial communication protocol developed by Siemens. It is designed to offer real-time communication between PLCs and field devices while supporting standard Ethernet infrastructure, making it suitable for both industrial automation and integration with IT systems.
Types of PROFINET:
-
PROFINET RT (Real-Time): Used for most industrial applications requiring fast, real-time communication.
-
PROFINET IRT (Isochronous Real-Time): Designed for high-performance, time-critical applications like motion control where precise synchronization is essential.
How PROFINET Works: PROFINET runs on standard Ethernet hardware and can handle both real-time control data and standard network traffic (like diagnostics or system management). It supports flexible topologies (star, ring, line) and can prioritize real-time data, ensuring reliable performance even in large and complex industrial systems.
Integration with PLCs: In a PROFINET-based control system, the PLC acts as a central controller, communicating with multiple field devices (sensors, drives, actuators) over Ethernet in real-time. This enables precise synchronization of devices like motors and drives, making it ideal for motion control applications.
Applications:
-
Motion Control: PROFINET IRT is commonly used in high-speed manufacturing, robotics, and CNC machinery where precise timing and synchronization are required.
-
Factory Automation: PROFINET RT is used in complex, interconnected industrial environments, allowing communication between PLCs, sensors, and enterprise systems (IT).
Advantages:
-
High-Speed and Scalable: Supports high-speed real-time data transfer (up to Gigabit Ethernet) and is scalable to large networks.
-
Ethernet-Based: Uses standard Ethernet infrastructure, making it future-proof and compatible with IT networks.
-
Real-Time Control: PROFINET IRT ensures that control tasks requiring strict timing (e.g., motion control) are handled with ultra-low latency.
Comparison of MODBUS, HART, PROFIBUS, and PROFINET
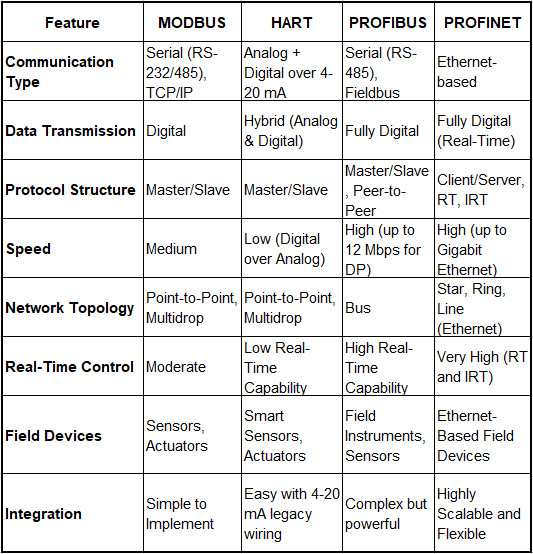
Conclusion
The choice of communication protocol depends on the specific requirements of your system. Here's a quick recap:
-
MODBUS: Ideal for simple, low-cost implementations where speed isn’t a critical factor.
-
HART: Excellent for leveraging existing analog systems while adding digital diagnostic capabilities.
-
PROFIBUS: Suitable for high-speed, real-time control in factory automation and hazardous environments.
-
PROFINET: The most advanced, offering Ethernet-based, high-speed, and scalable communication, making it the protocol of choice for modern industrial environments with a need for real-time control, motion synchronization, and integration with IT systems.